How process adherence at a fast-serve restaurant chain jumped 22% in just 90 days, fueling a nationwide rollout
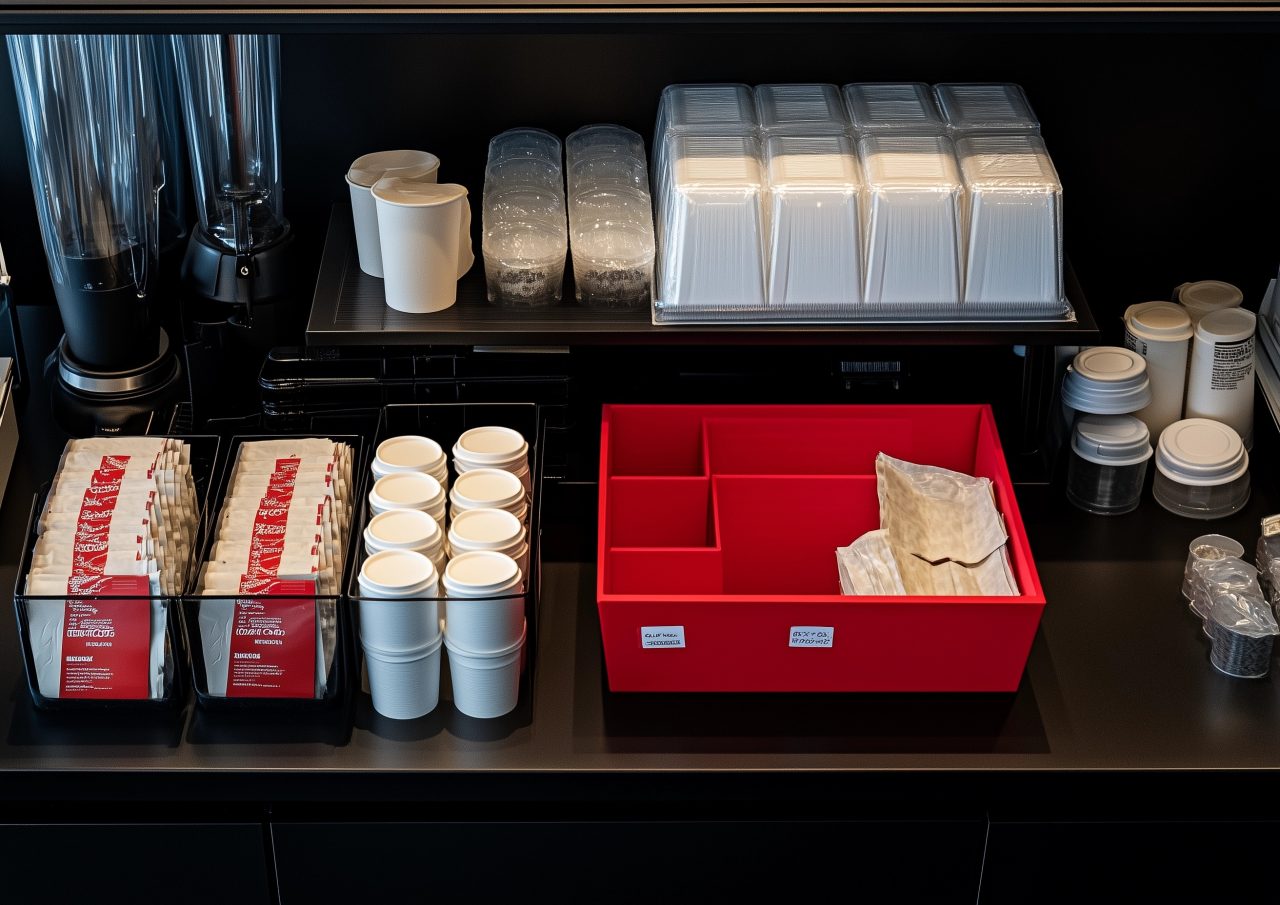
Customer background
An American fast-casual restaurant chain with over 530 locations serving nearly 2 million customers every week. Known for steakburgers and hand-dipped milkshakes, their brand depends on consistency, speed, and quality.
The business need
Consistency across shifts, locations and time is key success factor in the restaurant industry and was particularly important to the firm given their premium positioning.
Despite standardized training and checklists, manual audits and spot checks, it is often difficult to gain true visibility into the consistency of factors such as cook time, assembly sequences, sanitation procedures, drive-through speed and food safety compliance.
The firm required a real-time, scalable solution to monitor and improve process adherence without relying solely on in-person managers.
Challenges
Impact
Inconsistent process adherence
Reduced customer satisfaction
Increased operational costs
Resolution
The solution
The firm implemented a Computer Vision-based Process Adherence Platform in 20 pilot locations. Cameras were installed in strategic zones: kitchen prep, drive-thru, and food assembly lines.
The system used computer vision to:
- Detect process adherence within stores to
- Track key performance indicators: number of drive-through customers, drop-off rates, time at each location
- Detect key actions such as handwashing, food handling, and order assembly
- Monitor adherence to critical workflows (e.g., “meat on grill within X seconds”)
- Alert managers in real-time for missed steps or hygiene violations
- Aggregate data into dashboards showing compliance trends by location, shift, and process
Business results
Within just 90 days:
- Process adherence improved from 72% to 94% in pilot stores
- Drive-thru order errors dropped 28%, leading to fewer remakes and improved throughput
- Average service time improved by 17 seconds per order, boosting daily capacity
- Customer satisfaction increased by 12%, according to post-visit surveys
- Employee training time reduced by 22%, with the help of visual feedback loops
- Labor efficiency increased by 8%, as less time was spent correcting mistakes
- The success of the pilot led to a full rollout across all locations,
- Operations teams use data from their Viso application to continuously optimize workflows, reward high-performing teams, and proactively catch process drift.