Leading Global Food Retailer Enhances Safety with Viso AI
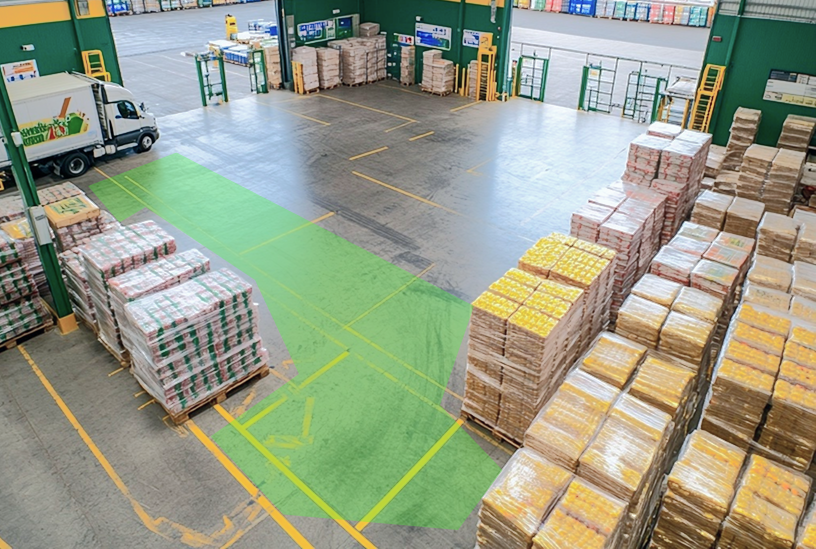
Customer background
Operations leaders at one of the world’s largest Food and Beverage companies who employ over 100,000 staff across 50+ countries approached Viso on the topic of safety and compliance within their production facilities and distribution centres.
The business need
The customer had three main goals:
- Enhance Workplace Safety and Compliance: Taking a proactive approach in enabling QHSE teams to maintain rigorous safety standards
- Improved Operational Oversight: QHSE, compliance and operational teams looked to understand the true scale and scope of incidents, near-incidents and wider contributing factors to support proactive action toward zero incident goals.
- Data-Driven Decision Making: QHSE teams looked to gain real-time insight into safety compliance, comparative performance across sites to understand the impact of process interventions, training investments and site layout optimizations.
In a solution, they sought something scalable across their global sites while being configurable to unique local requirements and allowing extension over time to additional use cases outside of Health and Safety.
Challenges
Impact
Inconsistent safety monitoring across global sites
Lack of real-time visibility into incidents and near-misses
Missed opportunities for process improvements
Increased downtime due to unaddressed safety risks
Resolution
The solution
Two pilot sites were selected, with the below initial applications built on Viso’s end-to-end computer vision platform:
- Restricted Area Monitoring: Alerts triggered when individuals entered unsafe areas around machinery. An incident center allows surfacing of general trends and root causes from anonymized incident clips, informing process improvements
- Forklift Near-Miss Detection: Previously only incidents triggered manual reporting; Viso enabled insight into the previously unknown scale of near-misses.
To enable ongoing customization to the particulars of global sites, Viso trained factory-based teams to use the intuitive tool. This will also allow them to build and scale new applications across sites going forward.
Business results
The custom gained:
- Enhanced safety and compliance
- 24/7 real-time visibility and comparability across global operations
- Reduced risk of incident-related downtime
- Faster improvement cycles through a culture of data