In industrial environments – whether in manufacturing, logistics, construction, or food services – safety and precision are mission-critical.
Every process, from material handling to machine operation, carries the potential for risk. A blocked emergency exit, an overlooked safety step, or a fatigued operator can disrupt workflows or lead to serious incidents.
Despite longstanding investments in Lean principles, Six Sigma, and ISO compliance, operational safety and precision often lag due to fragmented oversight and reactive reporting systems. But this is changing.
AI Vision has emerged as a pivotal enabler: embedding real-time visibility and intelligence directly into the flow of frontline operations.
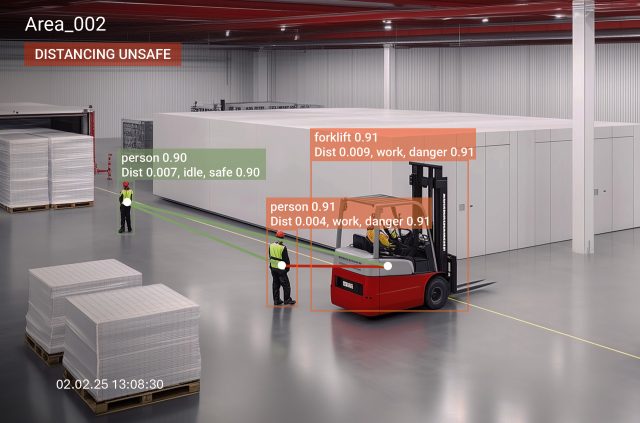
From risk to ROI: a step-change in safety and precision via AI Vision
Traditional safety management tends to rely on scheduled inspections, periodic audits, and after-the-fact incident analysis. These methods fall short in today’s always-on operational environment. They lack the safety and precision demanded today.
AI Vision, powered by computer vision models and real-time data processing, is bridging the gap, and unlocking safer operations. Instead of isolated checks, it offers continuous, automated monitoring of critical activities: flagging anomalies, non-compliance, or risk conditions as they arise.
‘Eyes that never blink’ empower production teams to monitor conditions across the line in real-time. By deploying models trained to detect non-compliance, unsafe behavior, and equipment misuse, companies can prevent incidents before they interrupt and damage operations and workers.
Some of the most impactful use cases include:
- Forklift and vehicle accident prevention: continuous monitoring for unsafe driving, averting near-misses
- Blocked path detection: automatically identifying obstructions that can delay material flow or create safety hazards
- Operator readiness: verifying machine operators are present, attentive, and properly equipped before each cycle begins
- Multi-operator task compliance: confirming two-person rule adherence for hazardous lifts or machine servicing
- Confined space monitoring: counting personnel and identifying crowding risks in restricted zones
Across these scenarios, companies deploying AI Vision to improve safety and precision observe reported improvements such as:
- 50% drop in vehicle-related safety events
- 60% decrease in near-miss incidents
- 75% fewer restricted zone intrusions
- 65% reduction in liability exposure for high-risk tasks
These capabilities not only mitigate safety risks but also yield measurable benefits: reduced downtime, fewer product quality issues due to operator fatigue, and lower incident-related costs.
For leaders focused on Overall Equipment Effectiveness (OEE) and operational throughput, this is where safety becomes a strategic lever, not just a tick box compliance task.
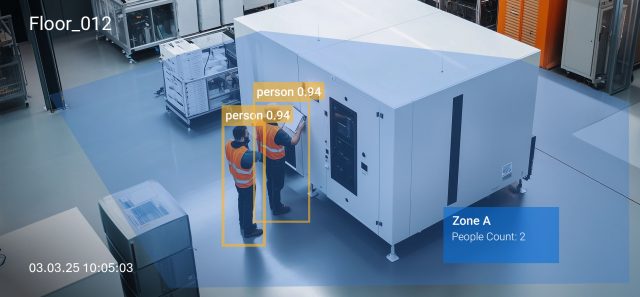
Smarter safety, stronger operations
AI Vision reframes safety as a dynamic performance metric rather than a reactive checkbox. Systems can now log and categorize safety events – even near-misses and protocol deviations that might have previously gone unnoticed.
This richer visibility allows for pro-active interventions to improve safety and precision:
Shift leaders can analyze behavior trends and adjust rotations or procedures to reduce fatigue-related errors
Health and safety managers gain timestamped evidence for root-cause investigations and can better prioritize retraining
General managers can correlate safety patterns with production bottlenecks or equipment issues, enabling smarter investments and process improvements.
Ultimately, these insights help organizations foster a culture of continuous safety improvement, where frontline teams see risk detection as fair, transparent, and collaborative.
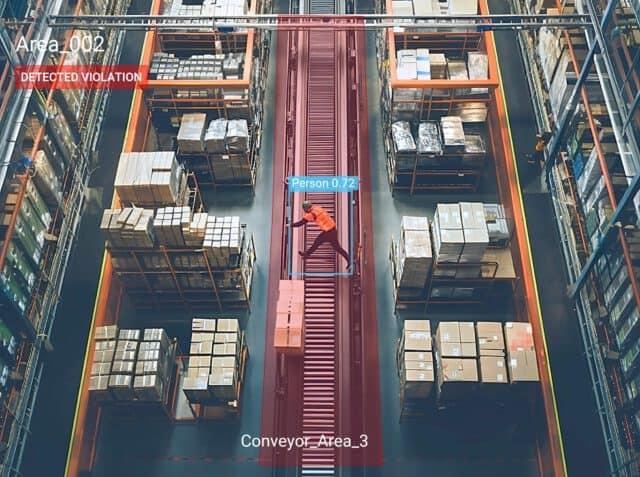
A practical path toward zero harm
What makes AI Vision particularly compelling is its adaptability.
Organizations don’t need to discard and replace existing infrastructure or retrain entire workforces overnight. Most modern AI Vision solutions integrate with existing camera networks and allow modular rollouts.
This means teams can start with focused use cases – like monitoring high-risk machinery or ensuring PPE compliance – then scale to broader applications such as site-wide hazard detection or vehicle-pedestrian interaction zones.
Implementation timelines are often measured in weeks, not quarters, with ROI showing up in the form of reduced claims, shorter stoppages, and improved worker confidence. AI Vision accelerates the path to zero harm.
Final thoughts: safety and precision on-the-line
For industrial leaders, safety and performance are no longer separate domains.
As Vision AI becomes more accessible and scalable, it offers a rare opportunity: to transform safety from a cost center into a driver of operational excellence.
By turning passive footage into actionable intelligence, AI Vision empowers teams to prevent risks before they escalate, reinforcing safe behaviors in real time. And it’s not just about reducing harm.
AI Vision is driving a new era of safety and precision. It is about raising the bar for how safe, efficient, and resilient modern operations can be. One where uptime and worker protection go hand in hand, and every shift can end as safely as it begins.