Computer vision (also known as AI Vision) enables the pursuit of zero downtime on production lines. It does so by detecting hazards like blocked exits, missing machine guards or unsafe behaviors in real time, preventing incidents before they occur.
Zero downtime: why it matters
Every safety failure can trigger downtime, injuries or fines. AI Vision helps mitigate these risks, reducing costly interruptions and enabling continuous, safer operations. Achieving zero downtime isn’t just about efficiency and profitability: it also means zero harm to workers.
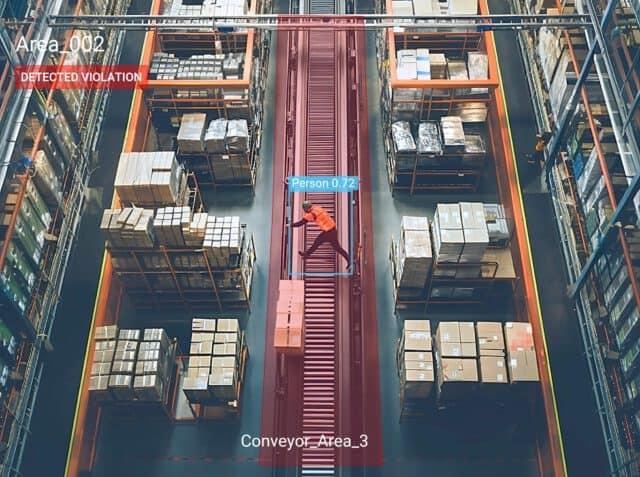
Safety and continuity on the line
Every production line operates under pressure: to increase throughput, reduce delays and ensure worker safety. But the margin for error can increasingly be razor thin.
One misstep – an unguarded machine, an obstructed emergency exit or a safety lockout failure – can halt operations, harm workers or lead to regulatory penalties.
Unplanned downtime due to safety incidents remains a critical threat.
Studies show it can reduce output by 20-30%, with costs running into the millions of dollars annually. This creates a pressing need for smarter, more pro-active safety systems. Manufacturers need systems that detect issues before they escalate and integrate safety oversight into the rhythm of production.
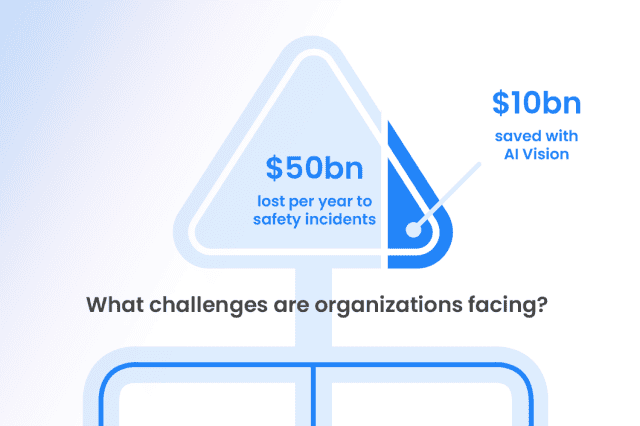
To learn more about the potential computer vision has to transform workplace safety (and see the rest of the above infographic!) please check out our HSE explainer.
Seeing more, sooner: how Vision AI works
AI Vision deployed through industrial cameras is helping to close this gap. By turning passive video feeds into intelligent monitoring tools, every part of the production line can be transformed into an actively observed environment.
Using trained models, AI Vision can:
- Identify blocked emergency exits and trigger alerts to clear them in real time
- Detect missing machine guards or covers before equipment starts
- Flag unauthorized or unsafe access during machine operation cycles
- Monitor operator behavior near critical or restricted zones
- Protect workers from near-misses with predictive analytics
Unlike traditional safety monitoring, which relies on human checks, manual audits, or post-incident reviews, AI Vision offers instantaneous, 24/7 situational awareness. This awareness in turn now ensures corrective action can be taken in seconds, rather than hours or even days.
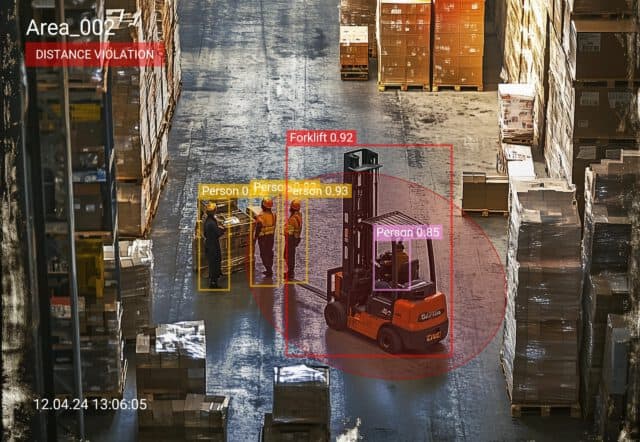
Real-world impact and ROI
These benefits are no longer theoretical.
Organizations deploying AI Vision have reported:
- 70% reductions in downtime caused by zone intrusions and unsafe behaviors
- Significant cost savings – up to $100,000 per year – through avoided fines and halted production
- Fewer audit failures and OSHA citations due to real-time documentation
- Improved compliance with safety related standards such as ISO 45001 (occupational health and safety)
Each incident avoided preserves not just safety but crucially also performance.
One emergency stop may cost hours of lost production, while an unreported hazard could lead to injury and litigation. By preventing issues at the source, Vision AI offers a compelling business case: lower risk, higher efficiency.
From reactive to proactive safety
What sets AI Vision apart is not just its ability to detect: it is how it empowers teams with real-time visibility and insight. Every flagged event is logged, timestamped, categorized and stored, accessibly, in a central dashboard.
This creates a data-rich environment for HSE leaders and operations teams to analyze safety performance across shifts, zones and facilities. Recurring issues – like repeated obstructions in a walk path or consistent misuse of a machine – can be tracked over time, allowing for targeted intervention and retraining.
Moreover, this approach strengthens compliance to ISO standards and more.
When safety inspectors request proof of clear emergency exits or use of proper guards, time-stamped visual evidence can be produced instantly. This slashes audit prep time, boosts transparency and bolsters regulatory confidence.
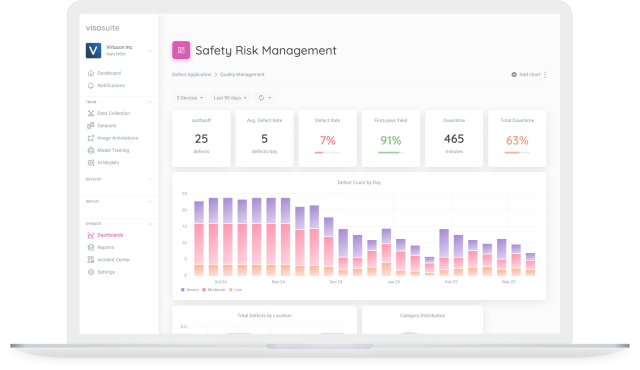
Streamlining the path to safer production
Contrary to assumptions, implementing AI Vision does not require a major overhaul. The system is typically deployed using existing camera infrastructure and it integrates with familiar platforms. These integrations with manufacturing execution systems (MES) and all forms of EHS software, ensure a low-friction and rapid adoption process.
Businesses usually begin with a focused pilot: a single production line, a high-risk work cell, or an area with repeat violations. Based on early results, the program can then be scaled site-wide or even enterprise-wide, often achieving full rollout within a few months.
This phased approach means real results – less downtime, fewer hazards, improved compliance – can start to be seen in just weeks, not lagging until the next quarter.
Building a culture of prevention
AI Vision does more than automate safety: it can be a transformative shift in mindset.
It enables teams to focus on prevention, not reaction; on systemic improvement, not one-off fixes. It enhances the roles of frontline safety professionals by giving them tools to act earlier, with greater precision, and more confidence.
For senior HSE leaders, it provides a strategic layer of assurance: knowing that every shift, every process and every safety-critical area is under continuous watch. It creates not only safer outcomes, but a resilient, safety-first culture where incidents are rare, not routine.
Final thought: towards zero downtime and zero harm
In today’s complex industrial environments, downtime is too expensive and injuries too unacceptable to remain dependent on outdated safety models. AI Vision offers an evolution – moving from limited oversight to intelligent, automated protection.
It bridges the gap between real-time detection and long-term safety strategy, turning every camera into an ally, every alert into a safeguard, and every avoided incident into measurable value.
The path to zero harm and zero downtime no longer starts with hope or unfounded optimism: it truly begins with visibility.
For those adopting this technology today, Vision AI is already delivering exactly that.