Using computer vision, various industries can predict and detect heavy machinery breakdowns by monitoring early signs of wear and tear, and avoid costly breakdowns. These Computer Vision systems can continuously monitor machinery and efficiently recognize gradual wear on machinery components that might not be visible to the human eye.
The Need for Computer Vision
In traditional methods dedicated teams are tasked with monitoring heavy machinery, which is time time-consuming process, and cannot be done continuously, which results in missing signs of breakdown, that could have been prevented.
Computer vision solves this problem, it not only runs continuously but also is highly accurate at detecting signs that if often invisible to the human eye. Additionally, the machines don’t need to be stopped for inspection, but they can keep running while the system monitors machinery. This reduces downtime and also improves the life span of heavy machinery. These systems are highly accurate at detecting cracks or deformation, for example, a conveyor belt with minor surface abrasions detected early through visual analysis can prevent larger tears or shutdowns.
Additionally, these systems also monitor machinery movement and flag any kind of unusual behavior that might indicate malfunctioning.
These systems capture visual data to assess the state of various components, such as gears, belts, and bearings, enabling real-time analysis without halting operations.
Technical Viewpoints
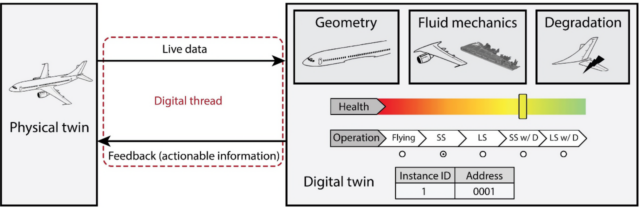
The Computer Vision system used for the predictive maintenance of heavy machinery involves a sequence of steps:
- Installed Cameras: Different types of cameras are installed within the machinery and in the area where machines operate. These cameras can be a combination of standard cameras and infrared cameras. Standard cameras detect machinery movement, while infrared cameras detect abnormal heat signatures in components.
- Environmental sensors record environmental conditions such as temperature and humidity. This is crucial for allowing machinery to work optimally.
- Deep Learning Models: These models identify patterns in images and data from various sensors and process them to detect key features that help predict wear and tear or abnormal movement by machinery.
- Edge Computing and Cloud Storage: These systems enable Deep Learning models to run and monitor machinery. Cloud storage is used to store and access key insights about machinery, from anywhere in the world.
Exemplary Industry Use Cases
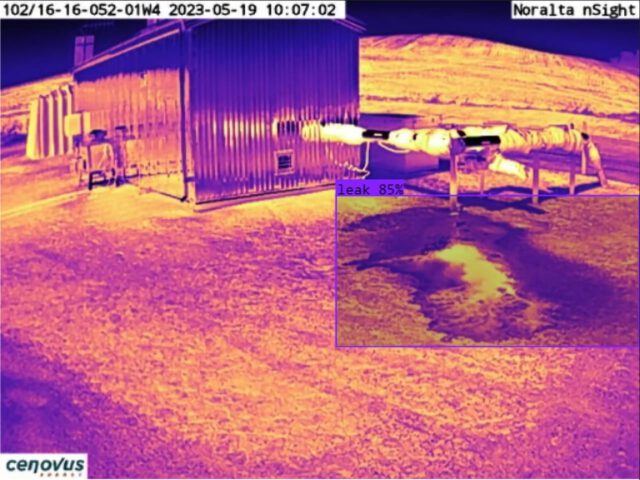
Predictive maintenance and monitoring of heavy machinery using Computer vision severa use across several industries:
- Mining Industry: Monitoring the structural integrity of excavators, dump trucks, and conveyor belts. High-resolution cameras paired with computer vision algorithms detect cracks, wear and tear, or misalignments in machinery. Thermal imaging is used to identify overheating components.
- Oil and Gas Industry: Inspecting drill bits, pipelines, and valves for signs of corrosion, leaks, or physical damage. Computer vision systems analyze images of machinery and pipelines to detect rust, cracks, or deformations in real-time. Infrared imaging detects leaks by identifying temperature anomalies.
- Manufacturing Industry: Monitoring robotic arms, conveyor belts, and assembly line equipment. Cameras installed along the production line capture real-time footage. Computer vision detects misalignments, unusual vibrations, or wear on moving parts.
- Railway Industry: Inspecting train wheels, axles, and tracks for wear and tear. Cameras mounted on trains or along tracks capture images. Computer vision identifies cracks, flat spots on wheels, or damaged rail segments.
- Construction Industry: Monitoring structural components of cranes, bulldozers, and other heavy construction equipment. Visual inspections using drones equipped with computer vision detect cracks, bent structures, or loose bolts on equipment.
Business Value Proposition
Using Computer Vision for predictive maintenance provides several benefits to businesses, such as efficiency, automation, and better safety.
- Minimized Downtime: Proactively identifying issues before they cause machinery breakdowns ensures consistent operations. Reduces unplanned outages and keeps production schedules on track, leading to higher productivity and profitability.
- Cost Savings on Repairs: Early detection of wear and tear or defects allows for minor repairs instead of expensive overhauls or replacements. Lowers maintenance costs significantly and reduces reliance on emergency repair services.
- Increased Operational Efficiency: Computer vision systems work 24/7 and provide real-time insights, ensuring machinery is always in top condition. Improves overall equipment effectiveness (OEE) by optimizing uptime, performance, and quality.
- Enhanced Safety: Identifying potential hazards such as structural weaknesses or overheating components reduces risks to workers and infrastructure. Prevents accidents, reduces liability, and improves compliance with safety regulations.
- Scalability and Automation: Computer vision solutions can monitor multiple assets simultaneously without needing manual inspections. Frees up human resources for higher-value tasks and ensures scalability as the business grows.