AGVs, short for Automatic Guided Vehicles, are autonomous mobile robots that navigate through pre-determined routes within a workplace facility. These intelligent machines move goods and materials efficiently without human involvement. The technology is being revolutionized with machine vision technology, which helps the AGVs move through complex environments, detect objects, and help in making intelligent real-time decisions.
By equipping the AGVs with machine vision systems, businesses can optimize their warehousing processes, reduce human errors, and provide safer working conditions. It’s not unreal to say that the adoption of these driverless vehicles with machine vision is not just a trend but a necessity for companies aiming to stay competitive in a rapidly evolving market.
In this article, we will explore:
- Concept of Automatic Guided Vehicles (AGVs) and their role in modern warehousing
- Explanation of AGVs, types, and key components
- Impact of machine vision on AGV performance
- Benefits, real-world applications, and future trends in AGV technology
What are Automatic Guided Vehicles?
Automatic Guided Vehicles are driverless, automatically controlled vehicles designed to transport materials within a manufacturing facility, warehouse, or distribution center. The vehicle navigates through the set routes usually defined with wires, magnetic strips, or laser paths embedded in the floor. An AGV follows set paths around the workplace, and a computer centrally controls its movement to ensure effective and safe travel around a warehouse.
While the concept of AGVs dates back to the 1950s, rapid advancements in artificial intelligence, sensor technology, and machine vision have propelled these systems into a new era. Today’s AGV is not merely a preprogrammed machine running along a fixed path; it is a complex, adaptive system capable of interacting with its surroundings and responsive to all changes within that environment.
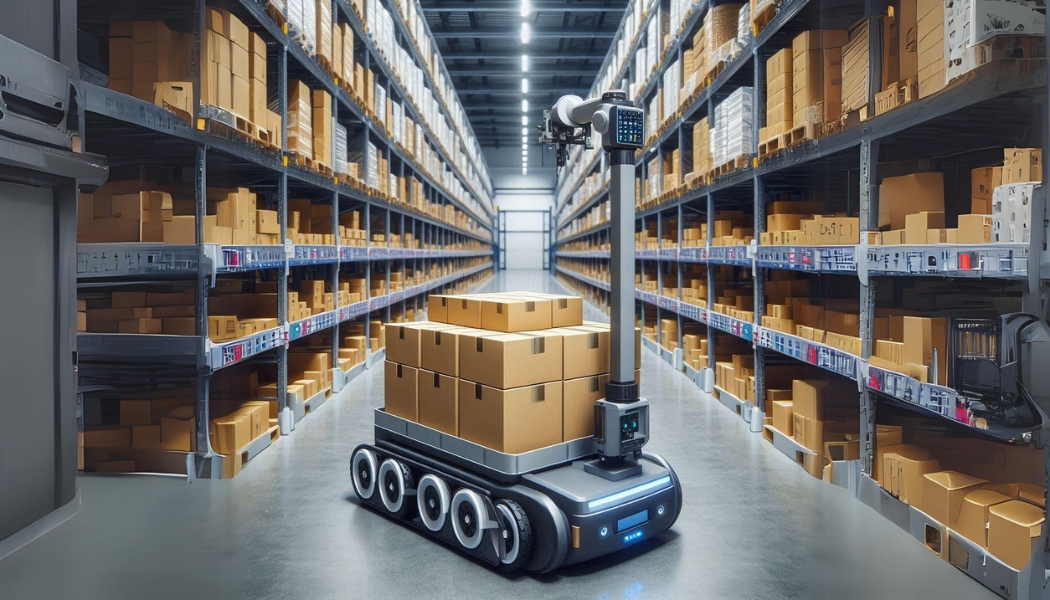
Types of Automated Guided Vehicles (AGVs)
AGVs come in various types, each designed for specific tasks:
Towing Vehicles
Towing AGVs are one of the oldest styles of autonomous robots and continue to be produced today. These vehicles are designed to pull trailers and can handle loads between 2,000 pounds and an impressive 160,000 pounds. It is also called “Tugger AGVs.”
They are a safer alternative to manually operating tuggers, especially in moving trailers or trains of trailers in a warehouse environment. Moreover, these machines have the capability of hauling several trailers together, which increases efficiency and safety in material handling operations.
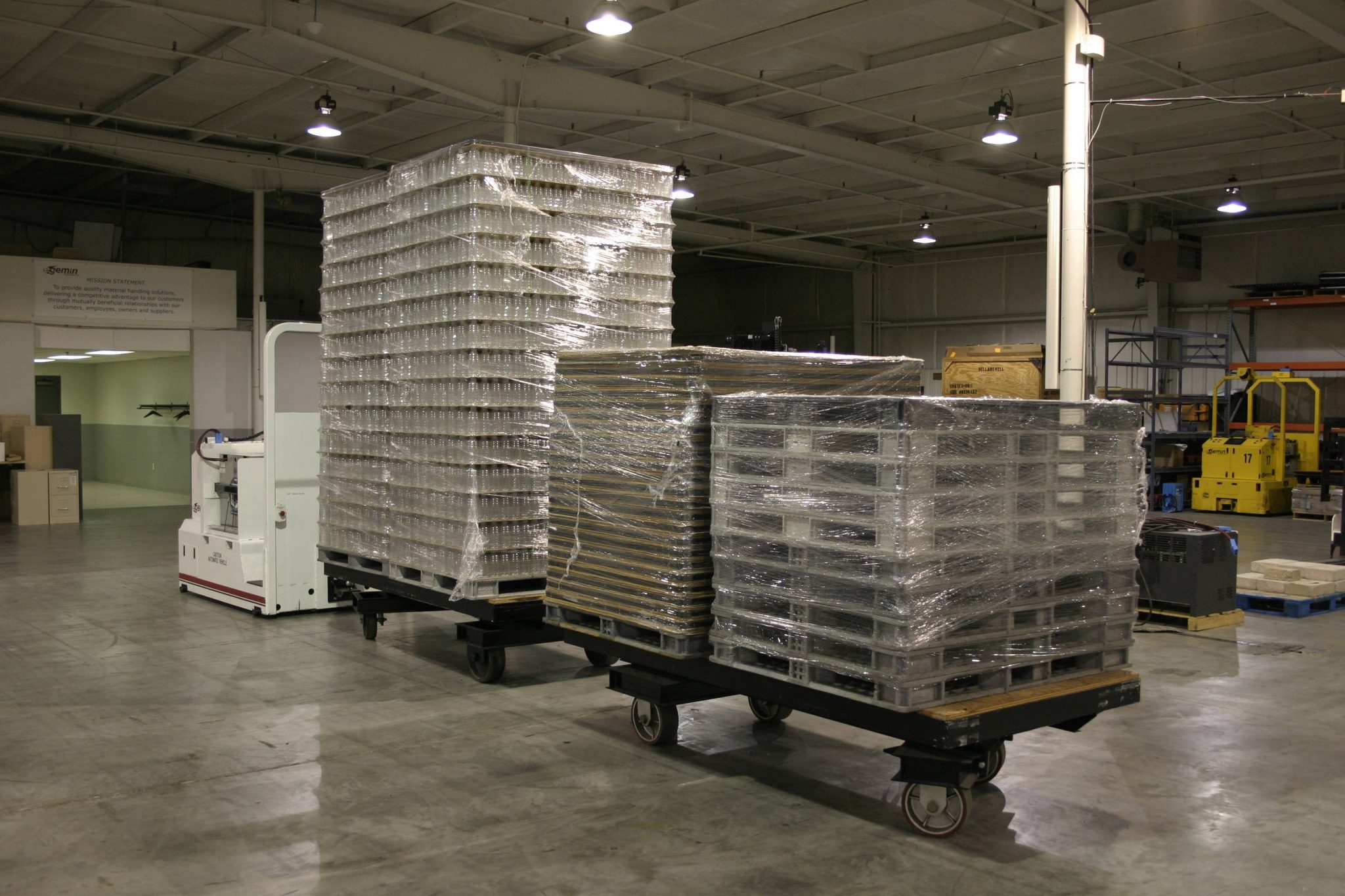
Unit Load AGVs
Unit Load AGV is a specialized vehicle with decks. They are designed particularly to handle unit loads effectively. Some of its types include lift and lower decks, powered or non-powered roller decks, chain or belt decks, and custom decks with multiple compartments. Unit Load AGVs normally have an automatic load-transfer feature, which makes them ideal for systematic material-handling environments that require very detailed transport and handling of materials.
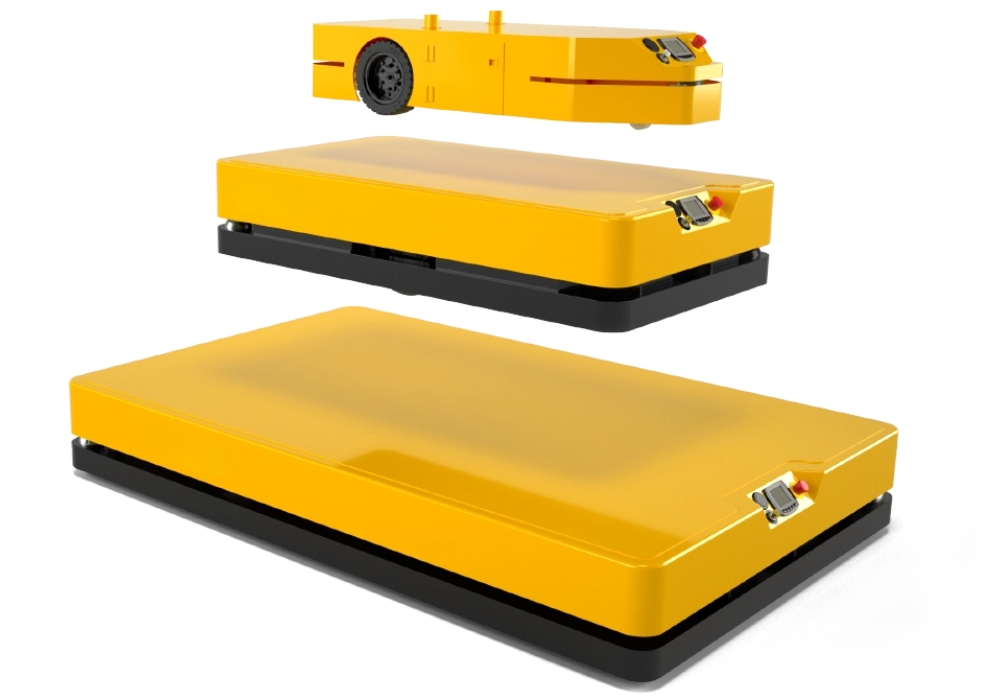
Light Load AGVs
Light Load AGVs are typically designed to transport small parts, baskets, or other light loads with capacities in the range of approximately 500 pounds or less. They find applications in light-manufacturing environments where smaller spaces and transport of small, lightweight materials are key requirements. For this reason, Light Load AGVs are mostly ideal for compact locations where bigger vehicles would not be necessary.
Assembly Line AGVs
Assembly line AGVs are an upgraded form of lift-carry load AGVs for light load suitable for serial assembly lines. Such vehicles are useful for moving small parts from one process point to another on an assembly line that is used in assembling products. Assembly Line AGVs work well in areas with less availability of spaces such as the light manufacturing environments. These compact vehicles ensure that parts are delivered to the right place at the right time.
Automated Guided Pallet Trucks
Automated Guided Pallet Trucks are designed to transport palletized loads to and from floor level. This autonomous feature eliminates the need for fixed-load stands. These AGVs streamline the movement of pallets within a warehouse and reduce the need for manual load handling. In short, we can say their ability to handle palletized loads directly from the floor to the warehouse racks makes them a versatile tool for modern warehousing operations.
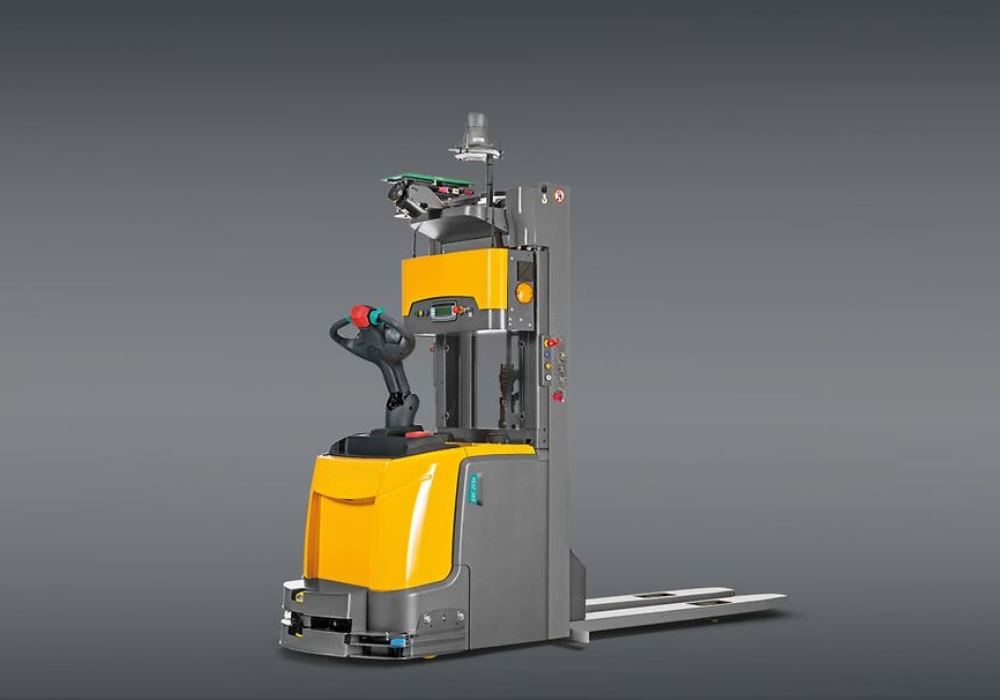
Automated Guided Hybrid Vehicles
These vehicles combine all the advantages of automated operation with the flexibility of manual control. These are adapted from standard man-on-board trucks and configured to perform fully automated operations or to be manually driven by a fork truck driver. This versatility makes them ideal for tasks such as trailer loading and delivering materials around warehouses. While they are most commonly equipped with forks, they can be customized to handle various load types, offering a flexible solution for different material handling tasks and needs.
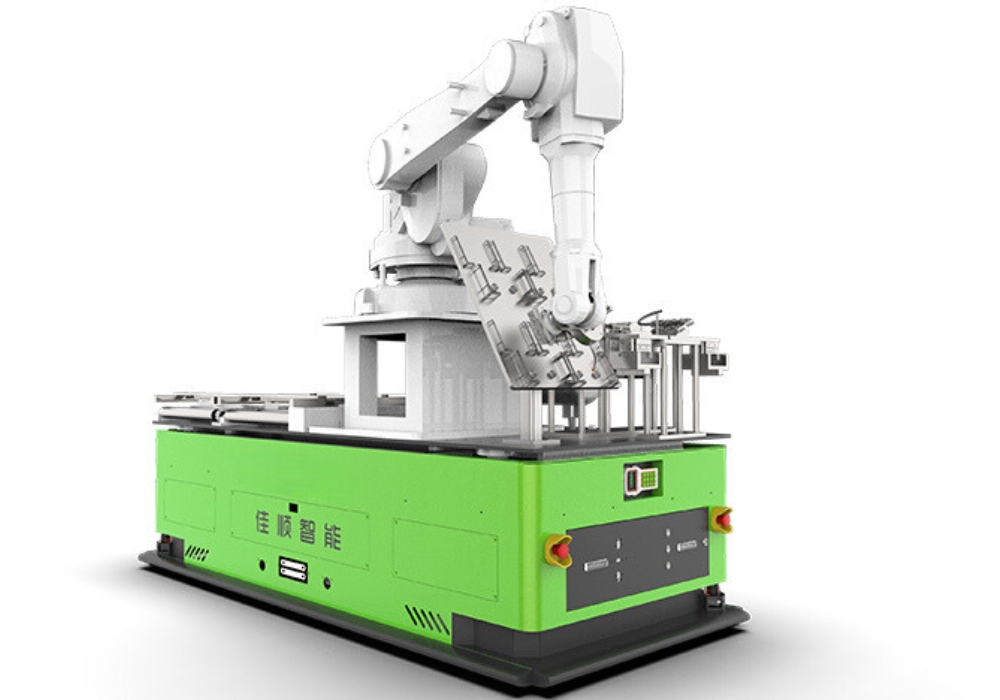
Key Components of AGVs
Automatic Guided Vehicles have four main components: the controller, sensors, actuators, and power system. Each component plays a crucial role in the AGV’s functionality and performance. Let’s discuss them in detail.
Controller
The controller operates as the brain for the AGV. It accepts information from sensors, processes it for decision-making, and commands the AGV operations. Its important parts include:
- Microprocessor: A high-level computer chip that interprets software and algorithms that are part of the AGV.
- Memory: Where it keeps maps, instructions, and operational data.
- Communication module: An interface that allows the controller to interact with a central control system or other AGVs.
- Software: This includes navigation algorithms, task scheduling, and safety protocols.
The controller interprets sensor data, plans the routes, and sends out the commands to actuators. At the same time, it also deals with the full-scale operation management problems of the AGV, such as battery management and error handling.
Sensors
Sensors act as the eyes and ears of the AGV, collecting data about the environment in which it is working. Commonly needed sensors for navigation, detection of obstacles, and safety features in an AGV include:
- Cameras: For vision-based navigation and object detection.
- Laser scanners: For accurate distance measurement, mapping, and obstacle detection.
- Ultrasonic sensors: For detecting close obstacles, especially when moving in very limited spaces.
- Encoders: Measure the rotations of wheels to calculate the position and speed of the AGV.
- Inertial Measurement Units (IMUs): Provide information on the orientation and acceleration of the AGV.
- RFID readers: Used to recognize tagged objects or locations within the warehouse.
These sensors work together to create a comprehensive understanding of the AGV’s environment and, in turn, accomplish safety and efficient navigation.
Actuators
Actuators are the components that allow the AGV to move and interact with its environment. They transform the controller’s commands into physical actions.
Here are some of the key actuators:
- Drive motor: It powers the AGV’s wheels or tracks for movement.
- Steering mechanisms: AGV steering components control the direction and maneuverability.
- Lift mechanisms: Commonly used in pallet trucks and forklift AGVs to raise and lower palletized loads.
- Brakes: Braking systems provide stopping power and hold the AGV in place when stationary.
Power System
The power system provides the energy needed for the AGV to operate. It typically consists of:
- Batteries: Most AGVs use rechargeable batteries, often lithium-ion for their high energy density and long life.
- Battery management system: A BMS monitors battery health and controls charging.
- Charging interface: It allows the AGV to connect to charging stations.
- Power distribution system: It helps deliver appropriate power to all components of the AGV.
Some advanced AGVs feature automatic battery swapping or opportunity charging systems that allow extended operation times.
Role of Machine Vision in AGVs
Machine vision is a technology that enables machines to receive and process visual information as humans do. This turns out to be one of the key features, especially for AGVs, for the systems to move around and detect objects. The key components for machine vision in AGVs are cameras, image sensors, and software algorithms for processing visual data. These systems allow the AGVs to “see” around them, thus facilitating real-time decision-making.
An example is an AGV fitted with machine vision that will enable it to spot obstacles on its way and hence change the route for safety and efficiency in performing its tasks. The single most important benefit of having machine vision on an AGV is improved navigation accuracy. Traditional AGVs navigate according to fixed paths or markers placed in certain locations. This could be very limiting in dynamic environments with routes that might be changing rather frequently.
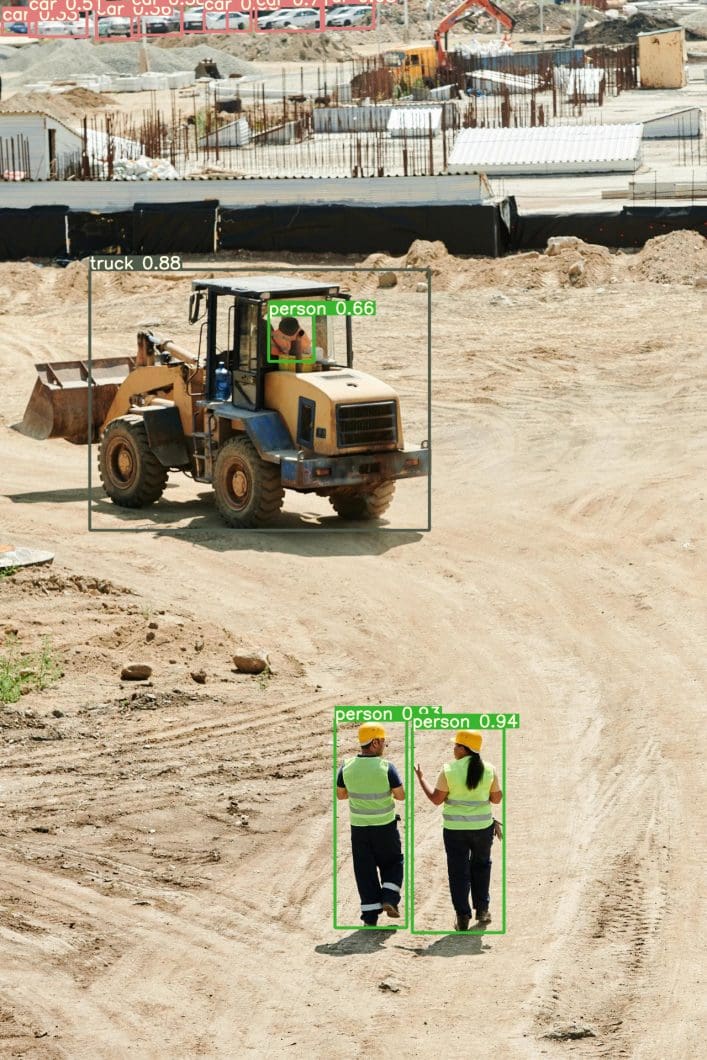
Machine vision enables AGVs to be more flexible in their path planning by recognizing visual cues in the environment, such as lines on the floor or certain landmarks in the warehouse. The object detection and recognition capabilities of the AGV are further enhanced through machine vision. This is very useful in environments where the AGVs are to interact with other objects by picking up some objects or avoiding obstacles. Machine vision systems can be programmed to recognize specific shapes, sizes, or colors, enabling AGVs to perform tasks with much enhanced precision.
Benefits of AGVs
The integration of AGVs in warehousing provides several benefits, hence improving efficiency, productivity, and safety.
Efficiency
AGVs improve warehousing efficiencies to a great extent through the automation of material handling that is otherwise done through human labor. This means that with AGVs, goods can be transported, pallets can be loaded and offloaded, and finished products can be translocated from one storage area to another without any interruptions for a break or due to shift changes. This ensures faster processing with no bottleneck in the workflow.
Additionally, AGVs are so reliable and provide consistent performance such that the work is always done correctly. Such consistency removes the randomness of human labor, and operations will be more predictable and maintainable.
Productivity
By automating repetitive and laborious jobs, the AGV releases human workers to engage in more valuable activities such as quality control, inventory management, and customer service. This increases the overall productivity of the workers and helps a business get more out of its workforce. In this regard, AGVs could be thought to perform a kind of 24/7 operation, increasing productivity.
Unlike humans, these vehicles do not need rest periods and are not subject to fatigue, meaning they can continue working without interruption. In industries where demand is high, or there is a very tight deadline in place, this form of continuous operation is particularly beneficial due to its constant flow of finished goods.
Safety
Safety is very important in any form of warehousing, and the use of AGVs makes the working environment safer. They assist in lowering the risk of workplace injuries regarding activities, which involve lifting heavy objects, excessive movements, or exposure to physical dangers. For example, AGVs as forklifts eliminate such incidents as collision and tipping when manually operating a forklift.
Further, AGVs are equipped with higher-level sensors and safety measures that enable the AGVs to sense and counter any barrier to movement including pedestrians. This will minimize the risks of possible crashes to create possibilities for AGVs to function in the same area as humans.
Real-world Applications
Automatic guided vehicles are utilized in different industries; however, warehousing and manufacturing industries have benefited the most from it. Let’s explore some real-world applications and specific examples of AGVs in action:
E-commerce Fulfillment Centers
Amazon: The e-commerce giant uses a fleet of AGVs called “Amazon Robots” in its fulfillment centers. These robots, acquired through the purchase of Kiva Systems (now Amazon Robotics), move entire shelving units to human pickers, significantly reducing walking time and increasing picking efficiency.
Automotive Manufacturing
BMW: At its Spartanburg plant in South Carolina, BMW uses laser-guided AGVs to transport car bodies between production stations. These AGVs can carry loads up to 2,000 kg and navigate with precision in tight spaces.
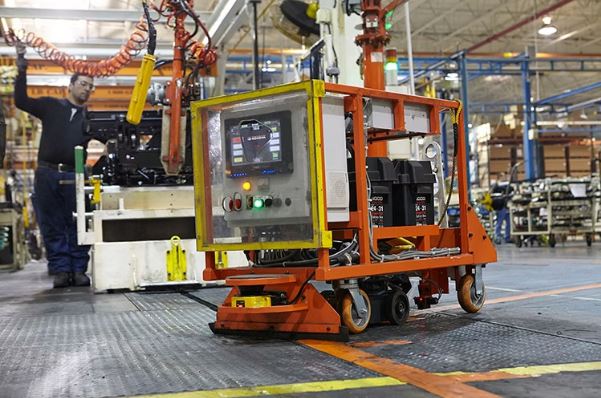
Food and Beverage Industry
Nestlé: In its Biessenhofen warehouse operations, Nestlé uses AGVs for pallet transport and storage. These vehicles are integrated with AVG navigation with 360° laser scanners. This has allowed the plant to streamline its flow of goods as well as reduce the amount of stock on its machines.
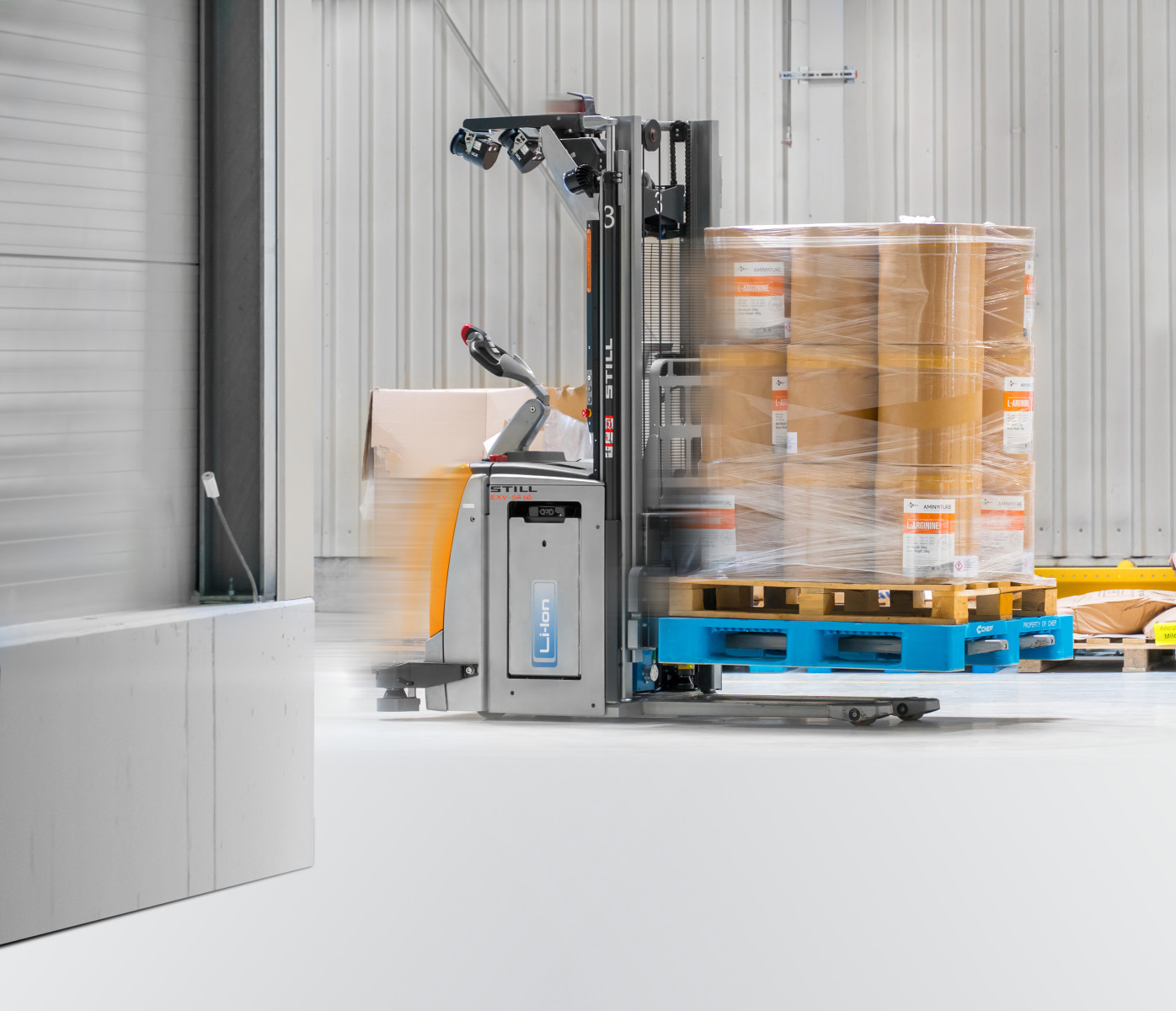
Future Trends of Automatic Guided Vehicles
The field of AGVs is rapidly evolving, with several emerging technologies poised to shape its future:
Artificial Intelligence and Machine Learning
AI and ML algorithms will enhance the intelligence and flexibility of AGVs. These technologies will allow the AGVs to learn from their previous operations, optimize their routes in real time, and even decide on complex tasks. Future AGVs will be able to predict traffic patterns, anticipate obstacles, and even forecast maintenance needs.
5G Connectivity
The actual deployment of the 5G network will radically transform AGV communications. The high speed and large volume of end-to-end connections will facilitate real-time synchronization of multiple AGVs and central control systems. This improved connectivity will facilitate more complex and dynamic warehouse operations.
Advanced Sensors and Computer Vision
Future advancements in sensors – LiDAR and 3D cameras will improve the AGV’s perception abilities. Advances made in the field of computer vision will let AGVs grasp their surroundings in an even better way, enabling more precise navigation and manipulation of objects.